Výroba segmentů Štvanické lávky
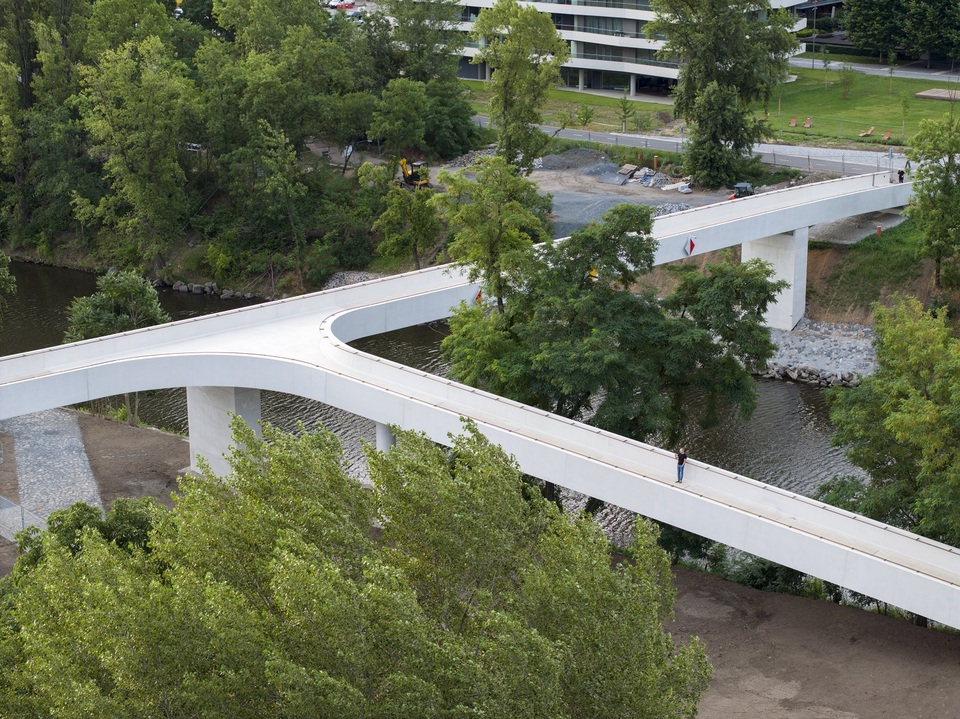
Foto archiv firmy
Autoři Štvanické lávky přišli s myšlenkou vytvořit souvislou spojitou a jednolitou linii, která propojí oba břehy a plynule odbočí na mezilehlý ostrov. Pro výrobce betonových prefabrikátů, kterým je společnost KŠ PREFA, to znamenalo najít hranici technických možností, s jistotou – alespoň malou – tyto limity popsat a podle toho jednolitou konstrukci „nakrájet“ na jednotlivé dílce.
Výsledkem tohoto hledání se stal prefabrikovaný segment délky bezmála šest metrů, šíře pět metrů, příčného řezu tvaru H a výšce 1,85 metru, který je i přes prostorové vedení lávky vždy přímý. Ďábelský detail spočíval ve faktu, že každý z 57 prefabrikátů byl tvarován trochu jinak, ale musel být odlit velmi přesně.
Geometrie segmentů
Potřeba sestavit na stavbě takovou polygonální segmentovou konstrukci v důsledku znamená, že je nutné, aby kontaktní spára byla co nejvíce kolmá na osu mostu. Současně je vedení předpínací výztuže v kanálcích uvnitř bočních parapetů řízeno jinou potřebnou geometrií než osa trajektorie mostu. Na stycích dílců byly osazovány (zabetonovány) speciální spojky kabelových kanálků, které prodlužují trvanlivost celé lávky. Nicméně „nakrájení“ původně spojité konstrukce způsobuje, že poloha těchto spojek je na čelech dílců proměnná a jejich úhel může být i mírně odlišný od úhlu „úklonu“ každého čela.
Forma
Ke zhotovení prefabrikovaných segmentů z UHPC (přesněji UHPFRC) popsaných dimenzí a parametrů bylo nutné překonat několik dalších překážek. Samotná materie čerstvého UHPC způsobuje, že nároky na formu jsou extrémní, tlaky vyvolávané čerstvou jemnozrnnou směsí (do dvou milimetrů) se samonivelační schopností jsou hydrostatické, obvykle o 50 až 70 procent vyšší než u běžného betonu, potřebná těsnost formy a její tuhost je s běžnou prefabrikací neporovnatelná.
Aby bylo možné použít otisk protiskluzné matrice na pochozím povrchu a zhotovit potřebná projektovaná zaoblení, byly segmenty betonovány v převrácené poloze. Celoocelová forma s hydraulicky odformovatelnými částmi s dvojitými čely umožnila úhlové natáčení kontaktních ploch a proměnné, ale velmi přesné osazování vložek pro smykové zámky a spojky kanálků, včetně úhlových odklonů. Při projektování formy byly současně upraveny výrobní výkresy vlastních segmentů. Bylo využito principu antisymetrie, kde obdobně jako při výrobě pomocí otisků na krátké výrobní dráze byly používány otisky stejných čel na předchozí a následující segment.
Pro atypické prefabrikáty osazené nerezovým kloubem pro zdvihané pole mostu byla forma rozšiřitelná, stejně tak pro segmenty nadpodporové. Pro dílce obsahující kotvy předpínací výztuže byla použita atypická čela a atypické vložené části. Vzhledem k velkému počtu segmentů a napjatému harmonogramu výroby byly zhotoveny dvě takovéto formy (obr. 1).
Postup výroby
Po každé betonáži byl vyrobený segment v určeném stáří přeměřen, projektant stanovil podle změřených odchylek od ideálního projektu tzv. kompenzace, tedy úpravy rozměrů v řádu milimetrů, které opravovaly nastavení dalšího čela.
Samotný systém měření geometrie stojí za zmínku. Protože obrys segmentu s ukloněnými čely je hranol s nerovnoběžnými podstavami, nemá smysl měřit celé délky hran. Ve formě byla s maximální přesností s použitím stěnových i prostorových úhlopříček stanovena středová rovina S kolmá na osu hranolu, která se pomocí drobných značek obtiskla do prefabrikátů a od ní byly měřeny vždy vzdálenosti k vrcholům čela. Ilustruje axonometrický drátový model (obr. 2).
Manipulace a otáčení
Vzhledem k subtilním rozměrům příčného řezu a k požadavku nezasahovat do pohledových ploch nebylo možné používat běžné způsoby manipulace s prefabrikáty, segmenty byly osazeny závitovými pouzdry v kontaktních čelech, vždy osm kusů na segment. Toto staticky neurčité zavěšení muselo využít na míru zhotovený systém kladek a vahadel, tak aby všechny závěsy byly rovnoměrně zatíženy; pro největší segmenty s hmotností přesahující 50 tun byly současně použity ty nejúnosnější dostupné na trhu.
Po výrobě v negativní poloze bylo nutné najít způsob otočení prefabrikátů s hmotností přesahující 50 tun (u největších dílců) tak, aby nedocházelo k poškození hran a vizuálně exponovaných ploch. Dílce byly otáčeny ve vzduchu pomocí soustavy řetězových závěsů na kladkách a vahadlech zavěšených na dvojici mobilních jeřábů (obr. 3 a 4).
Objem
Celkový objem segmentů z UHPC přesáhl 700 m3, celkový objem prefabrikátů 750 m3. Největší dílce s objemem bezmála 20 m3 s hmotností 50 tun a zabudovaným nerezovým kloubem jsou největšími prefabrikáty z UHPC vybetonovanými v Česku.
KŠ PREFA
www.ksprefa.cz

o tom vědět kliknutím na ikonku srdce.

Podobné články
< zpět na přehled článků